Closing Food Safety Gaps: The 3 Challenges of Food Traceability
Food safety is priority number one for the food and beverage industry as recalls have increased over the past decade. While food traceability regulations have been put into place to create efficient responses to outbreaks, most of the technology and processes that exist don’t solve all of the problems.
How do we close the gaps that still exist when it comes to traceability food safety? Before you can solve the problems, you must identify them. We’ll go through the three biggest gaps that still exist in food traceability and what can be done to fix the issues so you can ensure safety to the fullest extent possible.
Identifying Food Traceability Gaps
To effectively manage a contamination event, a fast response is needed. Although there are existing regulations in place by the FDA that establish traceability recordkeeping to enhance food safety measures, inefficiencies still exist. These are the top three most common issues putting your business, your customers, and the industry at risk.
1. Spotty Data
The number one thing preventing you from tracking and tracing food fast during a recall is insufficient data.
For instance, while the Produce Traceability Initiative, or PTI, is a universal standard, it’s still not universally adopted across the supply chain because of the costs to build an effective process. Not having this information creates incomplete data about a product’s origin, which is key during a recall and incident alert.
To track and identify food as it moves through the supply chain you have to have modern, unified data that can be understood and seen at every point in the supply chain. Where do you begin? First, you need to digitize your data. Paper trails, emails, phone calls, and faxes will only, slow down your food traceability system, putting you and your customers at risk.
Once you have digitized your data, then you can standardize it so everyone has access to the same data, but it needs to all reside in the same place. Through the unification of digital data -- everything from purchase orders to traceability to quality control -- insights & analytics can be shared instantly throughout the supply chain, allowing for a full picture of every product from farm to fork.
2. Limited Visibility
Being able to trace products throughout the supply chain requires full path visibility. Currently, because of the spotty data we discussed above, when a recall alert happens, each part of the supply chain acts using only the data they have available, which may only provide insight into a small part of the bigger problem.
Because data is not shared or unified, buyers and suppliers can’t truly gain the end-to-end visibility required to identify compromised goods and remove them quickly from the supply chain. Instead, the information and efforts are siloed, creating confusion and a lack of trust during a crucial time when everyone should be working together.
3. Lack of Coordination & Collaboration
Inefficient data and limited visibility contribute to the third problem that still exists with a traditional traceability food safety process: Coordination and collaboration.
The more complex your supply chain is, the more essential it is to coordinate across the entire path. But if you don’t have shared data or visibility, then mobilization is nearly impossible to achieve during a food safety event.
Industry experts shared the importance of this with Food Logistics, saying: “It’s so important now more than ever for supply chain partners to become more collaborative and work to understand what data needs to be collected and exchanged to ensure the safe passage of food from Point A to Point B.”
Traceability Food Safety Solution
A shared, modern, coordinated, digitized approach to traceability throughout the supply chain is needed to overcome these gaps. Traceability solutions, like iTradeNetwork’s, remove these obstacles from your process through a platform that offers:
- Faster recall management to ensure better public safety outcomes, brand protection, and reduced business impact
- Streamlined, immediate coordination that protects your buyer/supplier relationship
- Simple activation
iTradeNetwork has been a leader in perishables supply chain management for more than 25 years. Adapting to the changing times and creating a more efficient way to manage your supply chain is the main mission. Learn more about iTradeNetwork’s new food traceability technology here and find out how it can help you manage recalls instantly and close the gaps that put your company at risk.
Speak to an Expert
Take a closer look at the platform built for buyers and their trading partners
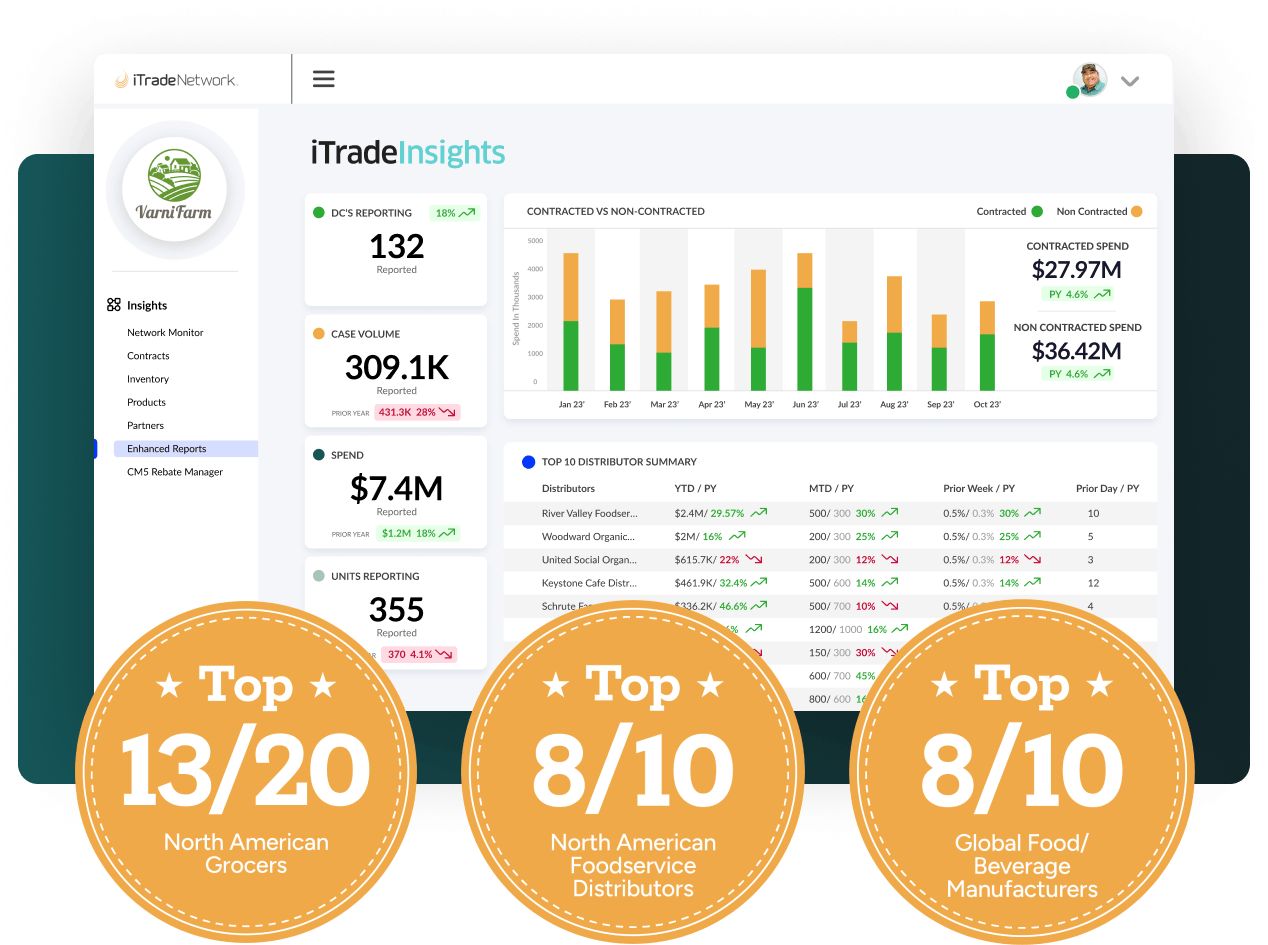
Closing Food Safety Gaps: The 3 Challenges of Food Traceability
Food safety is priority number one for the food and beverage industry as recalls have increased over the past decade. While food traceability regulations have been put into place to create efficient responses to outbreaks, most of the technology and processes that exist don’t solve all of the problems.
How do we close the gaps that still exist when it comes to traceability food safety? Before you can solve the problems, you must identify them. We’ll go through the three biggest gaps that still exist in food traceability and what can be done to fix the issues so you can ensure safety to the fullest extent possible.
Identifying Food Traceability Gaps
To effectively manage a contamination event, a fast response is needed. Although there are existing regulations in place by the FDA that establish traceability recordkeeping to enhance food safety measures, inefficiencies still exist. These are the top three most common issues putting your business, your customers, and the industry at risk.
1. Spotty Data
The number one thing preventing you from tracking and tracing food fast during a recall is insufficient data.
For instance, while the Produce Traceability Initiative, or PTI, is a universal standard, it’s still not universally adopted across the supply chain because of the costs to build an effective process. Not having this information creates incomplete data about a product’s origin, which is key during a recall and incident alert.
To track and identify food as it moves through the supply chain you have to have modern, unified data that can be understood and seen at every point in the supply chain. Where do you begin? First, you need to digitize your data. Paper trails, emails, phone calls, and faxes will only, slow down your food traceability system, putting you and your customers at risk.
Once you have digitized your data, then you can standardize it so everyone has access to the same data, but it needs to all reside in the same place. Through the unification of digital data -- everything from purchase orders to traceability to quality control -- insights & analytics can be shared instantly throughout the supply chain, allowing for a full picture of every product from farm to fork.
2. Limited Visibility
Being able to trace products throughout the supply chain requires full path visibility. Currently, because of the spotty data we discussed above, when a recall alert happens, each part of the supply chain acts using only the data they have available, which may only provide insight into a small part of the bigger problem.
Because data is not shared or unified, buyers and suppliers can’t truly gain the end-to-end visibility required to identify compromised goods and remove them quickly from the supply chain. Instead, the information and efforts are siloed, creating confusion and a lack of trust during a crucial time when everyone should be working together.
3. Lack of Coordination & Collaboration
Inefficient data and limited visibility contribute to the third problem that still exists with a traditional traceability food safety process: Coordination and collaboration.
The more complex your supply chain is, the more essential it is to coordinate across the entire path. But if you don’t have shared data or visibility, then mobilization is nearly impossible to achieve during a food safety event.
Industry experts shared the importance of this with Food Logistics, saying: “It’s so important now more than ever for supply chain partners to become more collaborative and work to understand what data needs to be collected and exchanged to ensure the safe passage of food from Point A to Point B.”
Traceability Food Safety Solution
A shared, modern, coordinated, digitized approach to traceability throughout the supply chain is needed to overcome these gaps. Traceability solutions, like iTradeNetwork’s, remove these obstacles from your process through a platform that offers:
- Faster recall management to ensure better public safety outcomes, brand protection, and reduced business impact
- Streamlined, immediate coordination that protects your buyer/supplier relationship
- Simple activation
iTradeNetwork has been a leader in perishables supply chain management for more than 25 years. Adapting to the changing times and creating a more efficient way to manage your supply chain is the main mission. Learn more about iTradeNetwork’s new food traceability technology here and find out how it can help you manage recalls instantly and close the gaps that put your company at risk.